Leading Techniques for Measuring Gauge Fillet Weld Accurately
Leading Techniques for Measuring Gauge Fillet Weld Accurately
Blog Article
Ingenious Techniques to Fillet Weld Evaluation and Testing: Enhancing Weld High Quality and Compliance Specifications
In the realm of welding, the quality and integrity of fillet welds play an important function in ensuring the structural sturdiness and reliability of various commercial components. With the constant drive for boosted performance and compliance with rigorous criteria, the expedition of ingenious methods to fillet weld inspection and screening has come to be essential. As sectors advance, the standard methods may no more be sufficient in meeting the demands of modern-day welding applications (Gauge Fillet Weld). By embracing cutting-edge modern technologies and methodologies, a brand-new horizon of possibilities arises in the realm of weld high quality evaluation and adherence to conformity requirements.
Advanced Non-Destructive Testing Methods
Making use of modern modern technologies, progressed non-destructive testing techniques play an important duty in ensuring the integrity and quality of fillet welds. These approaches, such as phased range ultrasonic testing (PAUT) and magnetic fragment testing (MPT), offer in-depth insights right into the weld's interior framework without triggering any type of damage to the product. PAUT, as an example, uses multiple ultrasonic components to check the weld from different angles, providing an extensive visualization of possible problems like absence of combination or cracks.
By employing these advanced non-destructive testing techniques, weld inspectors can accurately examine the quality of fillet welds, making sure compliance with market criteria and laws. The capacity to discover problems early on not only enhances weld quality but likewise prevents pricey rework or failures in structural integrity, underlining the value of these ingenious testing methods in welding inspections.
Robotics and Automation in Evaluation

The combination of robotics and automation has changed the examination procedure for fillet welds, improving efficiency and precision in quality analysis. Robotics supply precise control and repeatability in examining welds, guaranteeing regular and trustworthy outcomes. Automated systems can be configured to comply with particular evaluation paths, guaranteeing comprehensive insurance coverage of welds and decreasing the danger of human mistake.
Robotic inspection systems geared up with innovative sensing units can find and measure weld functions with high precision, providing in-depth information for analysis. These systems can identify issues such as splits, absence of blend, and porosity, making it possible for timely restorative activities to be taken. Additionally, robotics and automation permit real-time information collection and analysis, offering instant feedback to drivers and assisting in fast decision-making procedures.
Furthermore, the usage of robotics and automation in fillet weld evaluation enhances general performance by lowering evaluation times and raising examination throughput. By enhancing the evaluation procedure, producers can guarantee weld quality and compliance criteria are satisfied successfully, inevitably bring about set you back financial savings and improved product quality.
Making Use Of Artificial Intelligence for Evaluation
Synthetic knowledge plays a critical function in improving the performance and precision of evaluation in fillet weld inspection procedures. By harnessing the power of AI, inspectors can improve the evaluation of weld high quality and compliance criteria, causing much more reputable and exact outcomes. AI formulas can quickly refine large amounts of data from weld examinations, identifying defects or disparities that might be challenging to understand the nude eye. This sophisticated innovation enables real-time tracking of weld quality, permitting instant restorative actions to be taken if any kind of problems are discovered.
In addition, AI systems can gain from previous evaluation data, continuously enhancing their capability to determine possible flaws and inconsistencies in fillet welds. This flexible discovering capacity enhances the overall top quality control process, lowering the chance of human mistake and making sure that welds meet the required standards. By integrating expert system right into fillet weld analysis, markets can achieve greater degrees of performance, uniformity, and compliance in their assessment techniques.
Portable Equipment for On-Site Inspection
Enhancing field assessment efficiency, the fostering of mobile devices changes on-site analysis procedures for fillet welds. These devices provide adaptability and benefit, enabling examiners to carry out extensive assessments in various locations, consisting of remote or challenging settings. Mobile devices such as ultrasonic screening tools, magnetic fragment evaluation equipment, and digital radiography systems provide real-time information and high-resolution imaging capacities, allowing fast decision-making and instant responses on weld top quality.
One considerable advantage of mobile devices is their ability to enhance evaluation treatments, minimizing downtime and enhancing overall performance - Gauge Fillet Weld. Inspectors can quickly deliver these tools to various task websites, eliminating the requirement why not try these out for transporting heavy machinery or elements to off-site centers. Furthermore, the portability of these devices advertises cost-effectiveness by minimizing transport expenses and increasing evaluation timelines
In addition, using portable tools for on-site evaluation promotes aggressive quality control steps, as examiners can immediately identify and address any type of prospective welding defects or discrepancies. By incorporating these ingenious technologies right into on-site assessment techniques, welding specialists can make sure conformity with sector criteria and improve weld high quality, eventually leading to boosted structural honesty and safety and security in numerous welding applications.
Combination of Information Monitoring Solution
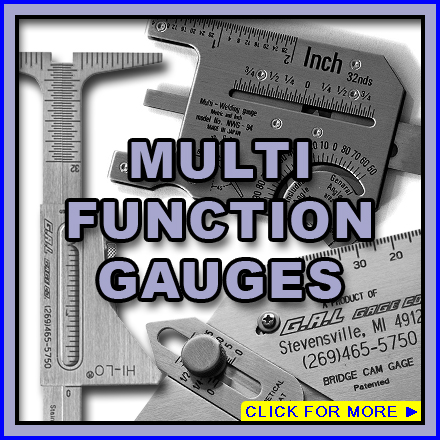
Having optimized on-site inspection procedures through the usage of portable devices, the next phase involves the smooth combination of data monitoring systems to additionally improve efficiency and data analysis abilities in fillet weld assessment and screening. By integrating information monitoring systems into the assessment process, companies can simplify information collection, storage, and evaluation. This combination permits real-time tracking of weld quality, prompt recognition of issues, and timely decision-making to remedy any concerns that may arise throughout the inspection process.
The assimilation of official website data administration systems allows smooth communication in between various stakeholders involved in the evaluation process, promoting collaboration and boosting overall high quality control procedures. Ultimately, the combination of data monitoring systems offers to boost the requirements of fillet weld assessment and testing, making sure compliance with sector regulations and boosting weld quality.
Conclusion
To conclude, ingenious methods to fillet weld evaluation and testing have substantially boosted weld top quality and compliance criteria. Advanced non-destructive testing approaches, robotics, automation, fabricated intelligence, mobile tools, and information management systems have reinvented the means weld inspections are conducted. By utilizing these technologies, sectors can guarantee that welds satisfy the required high quality requirements and policies, ultimately enhancing general effectiveness and security in welding procedures.
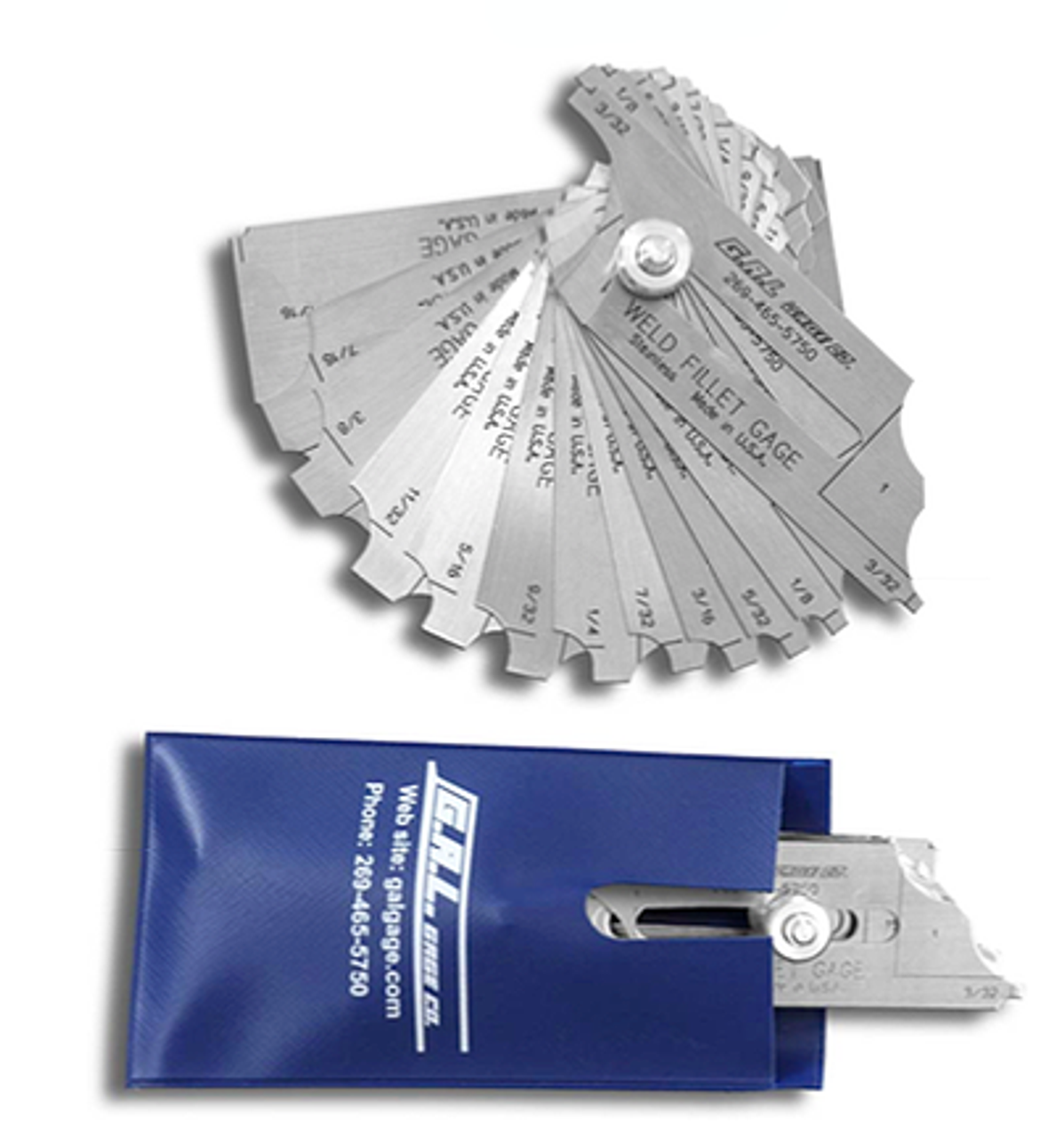
Having actually optimized on-site examination processes via the application of mobile tools, the next stage entails the seamless integration of data management systems to better improve efficiency and information evaluation capabilities in fillet weld assessment and testing. Inevitably, the assimilation of data management systems serves to elevate the standards of fillet weld evaluation go and screening, ensuring conformity with sector regulations and enhancing weld quality.

Report this page